1. PSA Process Introduction (압력차흡착법)
PSA(Pressure Swing Adsorption)는 기체혼합물을 분리하거나 특정성분을 제거시켜 기체를 정제하는데 사용되는 저에너지 분리공정이다. 저에너지 분리공정으로서 흡착제로 채워진 탑을 원료기체가 고압상태에서 통과하면서 특정성분들이 선택적으로 흡착되어지고 흡착이 잘안되는 성분들이 흡착탑 밖으로 빠져나온다. 압력을 떨어뜨려 탈착시키면 흡착제가 재생되고, 고압에서 얻어진 생성물의 일부로 낮은 압력의 탑을 세척시킨다. PSA공정의 설계 및 조업방식은 Feed의 종류와 원하는 Product에 따라 달라지므로 다목적으로 활용할 수 있는 PSA 공정 최적설계가 가능하다.
C.W.Skarstrom이 PSA조작에 의한 무가열 공기건조기를 개발한 이래로 PSA공정은 수소정제, 공기로부터 산소, 질소, 아르곤농축, CO제조, n과 iso-paraffin분리, 헬륨정제 등에 널리 사용되고 있다. 또한, Bulk Gas분리에 적절한 공정으로서 제철소 부생가스에서 CO회수, 천연가스에서 메탄분리, 메탄올 분해가스에서 CO회수, 에틸렌 off gas에서 H2회수 등 새로운 응용분야가 확대되고 있다.
PSA공정은 2개 이상의 흡착탑이 상호연결되어져 자동조절되어지는 밸브의 조작으로 흡착탑안의 압력이 높아지거나 낮아지고 시간에 따라 여러 방향으로 기체의 흐름이 변화되면서 조업이 이루어지게 된다. 따라서 흡착탑의 한 Cycle은 여러개의 step들로 구성되어지는데 step들의 구성 방식에 따라 기체성분들의 분리효과가 달라지게 된다. 또한 흡착탑 수를 늘려가면서 새로운 step들을 결합시켜가면 보다 효율적인 PSA공정으로 개선되어질 수 있으므로 궁극적으로 조업에 필요한 에너지를 절감할 수 있고 product의 순도와 회수율이 높아짐에 따라 공정의 경제성이 높아지게 된다.
분리조작은 산업공정 중에서 에너지를 많이 소비하는 주요한 부분의 하나로 그 중에서도 PSA 기술은 가열이나 냉각을 하지 않고 물질을 분리하는 공정으로 에너지 소비가 적고 설치, 운전 등이 간편하기 때문에 공기로부터 산소, 질소, 아르곤의 생산, 공기의 건조, 수소정제 등에 이용되고 있다.
2. Principle of PSA Process & Process Variables
2.1. Operating of PSA Process
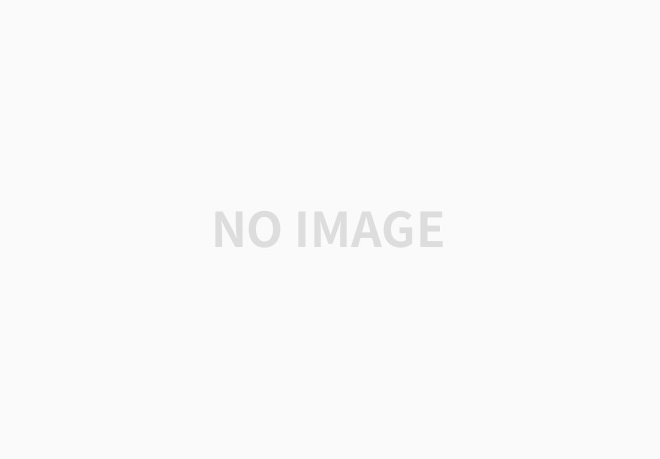
4개의 step으로 이루어지는 Skarastrom PSA Cycle을 기반으로 설명한다. Skarstrom PSA Cycle은 초기에는 heatless adsorption이라 불리워졌으며 일반적으로 Cycle 시간이 수초에서 수분 밖에 안되는 대단히 빠른 Cycle로 작동한다. Fig.1에서는 PSA Cycle이 어떻게 일어나느지 보여지고 있다. 흡착탑은 5A molecular sieve로 채워져 있어서 공기로부터 산소를 농축시키는데 사용된다. 5A molecular sieve에는 질소가 강하게 흡착하며 산소는 상대적으로 약하게 흡착한다. 한 Cycle을 구성하는 4개의 step은 다음과 같다.
- Pressurization Step
- High Pressure Production Step (Feed Step, Adsorption Step)
- Blowdown Step (Depressurization Step)
- Low Pressure Purge Step
2.2. PSA Process Thermodynamics
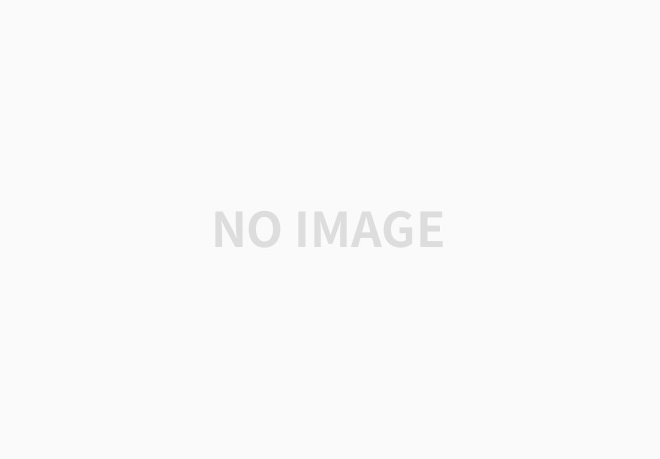
PSA는 거의 등온가동이라 할 수 있으며 등온흡착 특성에 주로 좌우된다. 일정한 온도에서 흡착된 양 q는 분압 p의 함수이며 분압이 △p만큼 변할때 흡착된 양은 △q만큼 변한다. (점A → 점B) 분압의 변화는 기체의 전체 압력이 변할 때나 (P1-P6) 혼합물 속의 농도가 변할 때 (△x) 나타나게 된다. Fig. 2에서 경로 AB1은 전체 압력이 P1으로 일정할 때 외부로부터 다른 비흡착성분의 주입으로 흡착성분이 희석됨에 따라, 즉 x가 떨어짐에 따라 일어나는 탈착에 해당된다. (Purge Step) 경로 AB2는 전체 압력이 P1에서 P6로 떨어짐에 따라 일어나는 탈착에 해당되며 결과적으로 x가 증가하는 농축 현상을 가져온다. (Blowdown Step) PSA는 열역학적인 관점에서 볼 때 성분의 분리에 수반되는 자유엔탈피의 증가가 단순히 압력의 증가에 의한 것이다.
2.3. PSA Process Variables
2.3.1. Bulk Separation인가, Gas Purification인가
생성물로서 얻고자 하는 기체성분이 원료혼합물 속에 약 20-80%정도 포함되어 있을 때 Bulk Separation이라 부르며, 공기로부터 산소농축 기체나 질소농축 기체를 얻는 경우가 이에 해당된다. 기체건조의 경우에서처럼 대단히 낮은 농도의 물질을 제거하는 정제공정들도 있다. 정제공정에서는 흡착탑ㅂ을 재생하기 전에 수시간 또는 수일씩 가동하는 경우가 있지만 Bulk Separation에서는 흡착Cycle이 대단히 짧아서 30초-5초마다 흡착, 탈착 및 재생단계가 반복되어진다. 흡착제가 포화되어져 강한 성분의 Breakthrough가 일어나는 시간이 짧기 때문이다.
2.3.2. 불순물
수분, CO2와 같이 강한 흡착능력을 가진 불순물들이 원료기체속에 들어 있으면 흡착제의 흡착능력을 크게 감소시킬 수 있다. 불순물이 쉽게 탈착되지 않는 경우에 더욱 심하다. 이러한 경우 원료기체가 PSA장치로 들어가기 전에 적당한 흡착제에 통과시켜 불순물을 제거시키는 전처리 방법이 사용된다. 한편 불순물이 거의 흡착이 되지 않는 경우에는 주성분의 생성물속에 불순물이 함께 포함된 채로 얻어지므로 생성물의 순도를 떨어뜨리게 된다.
2.3.3. 흡착제의 종류
흡착제 선정시 고려되는 사항
- 기체 혼합물 중 특정 성분에 대한 선택도
- 흡착능력(흡착제 무게당 흡착하는 기체의 부피)
- 흡착고도, 즉 PSA Cycle 도중 어느 정도 평형에 도달하는가
- 재생하기 전에 흡착제가 어느 정도까지 포화되는가
흔히 사용되는 흡착제들과 그 사용분야
- Activated Carbon, ZMS 3A; H2S, NH3, NOx 등의 제거
- ZMS 4A, 5A, Carbon Molecular Sieve(CMS); 공기분리
- ZMS 3A, 4A; 수소 정제
- ZMS 5A, 10X, 13X; Higher Paraffin의 분리
2.3.4. 흡착탑의 수
공장에서 필요로 하는 흡착탑의 수는 생성물의 원하는 순도와 기타 규격에 따르게 된다. 탑의 수가 많아질수록 밸브를 비롯해 부대 장치가 늘어나게 되어 Capital Cost가 높아지게 되며 가동조절이 복잡해짐에 따라 Operating Cost도 높아지게 되고 Start-up 비용과 건설비용이 늘어나게 된다. 일반적으로 탑의 수가 많아질수록 공정중에 발생하는 낮은 순도의 기체가 효율적으로 활용될 수 있으며 가동의 융통성도 커지게 된다. 따라서 비용의 절감과 가동의 효율성 사이에서 최적의 조건을 찾아야 한다. 실질적으로 대부분의 PSA 공정은 3개 이상의 흡착탑을 사용하고 있다.
2.3.5. 가동 압력
Cycle 중 낮은 압력 PL은 대기압보다 약간 높은 정도인 경우가 보통이다. 그러나 필요에 따라서는 진공세척을 사용하기도 하며, 이때에는 흡착탑 세척을 위해 생성물을 reflux 시키는 양이 줄어들거나 없어져 회수율을 높힐 수가 있다. 진공을 사용하면 전공펌프 투자비용이 들어가고 커다란 흡착탑에서는 진공에 도달하는데 오랜 시간이 걸리게 되어 Cycle 시간이 늘어나 시간당 생산량의 감소가 초래되기도 한다. Cycle 중 높은 압력 PH는 원료기체의 압력에 주로 의존되며 생성물의 원하는 압력에 다라 원료기체의 압력보다 높히거나 낮춘다. 수소정제에서는 50기압 정도까지 가동하고 공기건조에서는 5-8기압을 넘지 않는다. 생성물이 원료기체보다 낮은 압력에서 얻어지므로 나중에 압축시켜야 할 경우도 있다. 이러한 경우에는 원료기체 압력을 풀어 주면서 Blowdown Step때 탈착되는 생성물을 탑으로부터 밀어내기도 한다.
압력비 PH/PL이 높아지면 Molar Reflux Ratio는 일정하게 유지되면서도 reflux에 사용할 수 있는 기체의 부피가 늘어나 생성물 순도가 높아진다. 다르게 표현하면, reflux 기체의 부피를 일정하게 유지하면서도 Molar Reflux Ratio를 줄여주어 회수율이 높아진다. (Refulx ratio는 Low pressure purge 단계에 있는 탑으로 순환시켜 보내지는 고압 생성 기체의 양과 고압탑에서 얻어지는 기체 양의 비율이다) 최소 reflux에 대응하는 최소 압력비가 존재하며 비흡착 성분의 mole fraction의 역수보다 압력비가 커야한다. (최소 reflux비라함은 그 이하의 비로 reflux시키면은 세척이 불완전해 순수한 생성물이 얻어지지 않는 것을 가르킨다.) 선형 등온흡착인 경우에는 순수한 생성물을 얻기 위해 최소 reflux비에서, 세척하는 부피와 원료의 부피가 같으며 molar reflux ratio = PL/PH이 된다. 그러나 실제의 경우는 세척부피와 원료부피의 비가 1보다 커야한다.
2.3.6. 온도
대부분의 공정이 상온 근처나 원료기체의 온도에서 운전되지만 가동온도도 중요한 인자로 간주된다. 온도는 흡착제의 평형흡착 양, 흡착곡선 형태, 다른 성분들 사이 선택도, 흡착 kinetics 등에 영향을 준다. 예를 들어, 가동 온도가 높아져 특정 성분의 흡착이 무시될 정도로 줄어 들면 그 성분을 순수한 생성물로서 회수하기가 쉬어진다. 온도가 높아질수록 가동범위 내에서 흡착이 선형에 가까워지므로 탈착이 쉽게 일어나 kinetics가 개선되어지고 비가역 가동에서 더 벗어날 수 있다. 일반적으로 reflux ratio도 줄어들게 된다. 그러나 온도가 높아지면 흡착능력은 감소하므로 Cycle당 처리할 수 있는 원료의 양이 줄어든다.
2.3.7. 열효과
흡착할 때 열이 발생하고 탈착할 때 열이 흡수되는 열효과를 유리하게 이용하는 방법으로 기체흐름 사이에 열교환을 이용하는 여러공정이 제안되어 있으나 원료기체의 온도가 상온보다 많이 높거나 많이 낮을 때에만 경제적이 된다. 흡착탑들이 떨어져 있을 경우에 여러 탑들과 기체 흐름들 사이의 열전달을 효과적으로 도모하기 힘드므로 annular bed 형태로 열효과의 이용을 증진시킬 수도 있다.
2.3.8. 기체속도
등압단계의 기체속도는 보통 0.01-0.5m/s이며 흡착탑 내의 pressure drop에 관계된다. 흡착성분의 농도가 낮을수록 기체속도를 높힐수 있고 기체속도가 커집에 따라 기체와 고체사이 물질전달 효과가 좋아진다. 일반적으로 탑 내에서 기체의 평균 머무는 시간이 characteristic transfer time보다 커야지만 날카로운 흡착경계면이 얻어진다.
2.3.9. 흡착탑 형태
전형적인 흡착탑은 수직 형태로서 탑 밑에서는 우너료의 주입과 진공으로 빨아내는 것이 이뤄지고 탑 위에서는 비흡착성분이 나오게 된다. 수평형태의 탑을 사용하지 않는 것은 수평 위체에서는 흡착제로 탑을 채우거나 비우는게 어려울뿐 아니라 흡착제가 밑으로 가라앉아 수평탑 안의 빈 공간을 통해 기체가 흘러갈 우려가 있기 때문이다. 그러나 흡착탑의 높이가 대략 2m를 넘으면 흡착제의 강도가 약해서 부서지게 되므로 중간 중간에 추가의 지지대를 놓아야 한다. 탑의 높이에는 이런 제한이 있는 반면 탑의 직경은 클 수가 있다. 탑의 직경이 커지게 되면 탑 입구로 들어가는 원료기체의 분산이 탑 전면적에 걸쳐 골고루 일어나기 힘드르로 잘 고안된 distributor를 사용할 필요가 있다. 수평 형태의 탑은 공간 면적이 절약되고 설치, 유지 및 보수가 쉬우므로 간혹 사용되기도 한다.
2.3.10. 분리 결과의 평가 요소
PSA분리공정은 다음 세가지로 평가될 수 있다. (a) Product Purity, (b) Product Recovery, (c) Adsorbent Productivity. 한가지 이상의 성분이 회수될 경우에는 각 생성물에 대해 (a)와 (b)가 적용된다. Surge나 Mixing Tank를 사용하지 않는다면 PSA장치에서 나오는 생성물의 속도와 농도가 시간에 따라 변하므로 부피 평균한 값으로써 제품의 순도를 결정해야 한다. 제품의 회수율은 원하는 성분이 생성물로서 얻어지는 양과 원료 기체 속에 포함되어 있는 양의 비로 나타낸다. Adsorbent Productivity는 흡착제 단위 무게당 단위 시간당 생산되는 제품의 양 또는 원료의 양을 표시한다. 주어진 분리공정에서 원하는 제품의 순도는 미리 결정되어지며 사용되는 에너지 양은 회수율에 비례하고 흡착탑 크기는 Adsorbent Productivity에 반비례한다. 어떠한 PSA공정에서도 (a), (b), (c) 세가지는 상호 관계되어지며 변한다.
2.4. PSA Process Stages
2.4.1. Repressurization
가압은 원료기체로 할 수도 있고 다른 탑에서 나오는 고압 생성물을 이용해 할 수도 있다. 생성물을 이용해 가압하는 경우는 원료 주입과 반대 방향으로 수행하여 바로 앞 단계 때 Purge가 불완전하여 탑 안에 일부 남아 있는 강한 흡착 성분을 원료 주입 입구쪽으로 몰아 붙인다. 원료기체로 가압할 때 강한 흡착성분이 탑 내로 주입되는 것과는 달리 순수한 생성물이 들어오면서 가압되면은, 그다음의 Feed Step에서 강한 흡착성분의 Breakthrough가 일어날 때까지 좀더 오래 원료주입을 지속시키거나 기체의 통과 속도를 높혀줄 수 있는 장점이 있는 반면 생성물의 일부가 가압에 사용되므로 생성물의 손실이 늘어난다. 그러나 무게의 상반되는 효과는 대게의 경우 회수율을 높히는 결과로 나타난다. 가압에 사용하는 생성물을 Feed Step도중 고압 생성물을 별도의 저장탱크에 일단 받아 놓았다가 Repressurization Step이 돌아왔을 때 상요할 수 있으며 또다른 방법으로는 Feed Step에 있는 다른 흡착탑에서 나오고 있는 고압생성물을 직접 이용할 수도 있다. Pressure Equalization(PEQ) Step이 사용될 때에는 압력이 PEQ에 의해 PL로부터 어느 정도의 중간 압력까지만 높아지고 최종적으로 고압생성물 또는 원료에 의해 PH까지 높아지게 된다.
2.4.2. Blowdown
PH가 높을수록 Depressurization되는 부피가 증가하여 그 다음에 오는 Purge Step때 사용되는 비흡착 생성물의 Reflux를 줄일 수 있다. 즉 Purge기체로써의 손실이 줄어든다. 그러나 Blowdown(BD) 기체로써 손실되는 비흡착성분의 양이 늘어나므로 이 상반되는 효과에 의해 고압 가동의 이득이 어느 정도 상쇄되어진다. PEQ Step이 사용될 대에는 BD을 일부만 진행시켜 압력을 PH로부터 어느 정도의 중간 압력까지만 낮추고 이때 생기는 BD기체를 이용해 다른 저압의 탑을 부분적으로 가압을 한다. BD은 기보적으로는 Countercurrent하게 행해지지만 Countercurrent BD 직전에 Cocurrent한 Step을 삽입하는 경우도 있다.
2.4.3. Cocurrent Depressurization
원료주입이 끝난 직후 Cocurrent Depressurization (CD) Step을 삽입시키기 위해선 Feed Step을 Break Point보다 훨씬 이전에 중단시켜서 강한 흡착성분의 경계면이 생성물 출구로부터 멀리 떨어져 있어야 한다. CD Step이 끝난 뒤에는 통상적인 Countercurrent BD과 Purge에 의한 탈착 및 재생을 계속해서 진행시킨다. CD Step을 도입하면 강한 흡착성분을 높은 농도로 회수할 수 있게 되고 결과적으로 약한 흡착성분의 회수율이 증가하게 된다.
2.4.4. Pressure Equalization
한 흡착탑은 가압이 되어야 하고 다른 탑은 감압이 되어야 할 때 두 개의 탑을 연결시켜 압력이 같아지도록 하는 것이 Pressure Equalization(PEQ)이다. 이 Step을 도입하면 생성물이 손실되는 것이 줄어서 회수율이 높아진다. PEQ은 한 흡착탑과 그것의 압력에 가장 가까운 흡착탑을 연결시키는 방식으로 여러번에 걸쳐 일어나게 할 수 있다. PEQ은 탑의 어느 쪽 끝에서도 일어나게 할 수 있다.
2.4.5. Purge
고압의 순수한 생성물을 팽창시켜 낮은 압력의 흡착탑으로 보내 탑을 씼어주는 Purge Step은 효과적인 분리를 위해서 대단히 중요하다. 보통 원료주입 방향과 역방향으로 Purge시켜 원료 입구 쪽으로 강한 흡착성분들을 밀어내는데, 이는 다음 Cycle에서 생성물의 강한 흡착성분에 의한 오염을 막기위한 것이다.
2.4.6. Vacuum Regeneration
흡착탑을 재생시키기 위해 진공을 사용할 수 있다. 이것은 Purge Step을 대신해서 할 수도 있고 Purge Step에 덧붙여 할 수도 잇다. 진공조업을 하면 약한 흡착성분인 생성물 기체의 손실이 최소로 줄어들고 순도도 높아지는 반면 진공 System을 사용하는데 따른 단점이 생겨나고 흡착탑도 더 커지는 경우가 흔히 있다.
2.4.7. Purge by Strong Adsorptive
강한 흡착성분을 고압으로 집어 넣어 주면서 약한 흡착성분을 밀어내 주는 과정으로 일반적으로 원료주입과 같은 방향으로 행한다. 이러한 reflux 기체를 압축시키기 위해선 압축기가 필요하다. 이 방법을 쓰는 이유는 포화된 흡착탑 내부 빈 공간에 차 있는 원료기체가 분리성능에 제약을 주고 특히 강한 ㅅ어분의 순도를 높게 하지 못하기 때문이다.
2.4.8. Delay
어떤 공정에서는 탑으로 들어오고 나가는 기체의 흐름이 없는 delay step이 포함되기도 한다. 이 delay step 동안에 확산속도가 늦은 solute가 충분히 흡착 또는 탈착이 되며, pressure wave가 탑 내부를 이동할 시간이 주어진다. 또는 두개 이상의 탑이 여러개의 Step으로 연속적인 조업이 되는 Cycle을 구성하는데에 필요 되어지기도 한다.
2.4.9. Pretreatment
Zeolite에 강하게 흡착하는 수분이나 CO2는 공기의 분리뿐 아니라 다른 기체의 분리에서도 문제가 된다. 이들 성분은 쉽게 탈착하지 않으며 흡착탑 내에 축저이 되어 조업 중단을 야기시키기도 한다. 이 문제를 해결하기 위해 PSA System 외부에 전처리 탑을 부착시켜 PSA와는 별도로 재생시킨다.
2.5. 상업적인 공기분리 PSA Processes
2.5.1. 공기로부터의 산소분리
Cryogenic Process는 공기로부터 고순도의 산소, 질소, 비활성 기체를 대규모로 생산하는데 사용되고 있다.
2.5.2. 공기로부터의 질소분리
산소의 경우와 마찬가지로 질소의 생산규모가 작고 순도가 대략 99.7% 이하인 경우에 Cryogenic Distillation보다 PSA공정이 경제적이 된다.
REFERENCE
- PSA공정의 개발에 관한 연구, 한국과학기술연구원, 과학기술처
'둘 > [ Chemical Engineering ]' 카테고리의 다른 글
Entrainment(비말동반) in distillation (0) | 2022.01.13 |
---|---|
Sm3, Nm3, Am3 Energy Unit (0) | 2021.11.15 |
Absorption & Stripping (0) | 2021.10.19 |